از ترکیب دو یا چند ماده با یکدیگر به دست میآید. این تعریفی است که معمولا برای کامپوزیت ارائه میدهند. ترکیب سازنده کامپوزیت، از دو بخش اصلی که تقویتکننده و زمینه نام دارند، تشکیل میشود. زمینهی کامپوزیتها به سه دسته فلزی، پلیمری و سرامیکی تقسیم میشوند.
نوع زمینهای که در کامپوزیت استفاده میشود، در کاربرد آن تاثیرگذار است. کامپوزیت زمینه فلزی نسبت به دیگر انواع کامپوزیت ویژگیهای قابل توجهتری دارد. به همین خاطر تصمیم گرفتیم تا در مطلبی جداگانه به کامپوزیت فلزی، فرآیند ساخت آن و خواص منحصربهفردی که دارد، بپردازیم. تا انتهای این مقاله با ما همراه باشید تا کامپوزیت زمینه فلزی را بهتر و بیشتر بشناسید.
در فرآیند ساخت کامپوزیتهای زمینه فلزی (Metal Matrix Composite)، از یک قطعه فلزی مثل آلومینیوم به عنوان زمینه خود استفاده میکنند و الیافهای مختلفی مثل سیلیکون، به عنوان تقویتکننده با آن ترکیب میشوند.
کامپوزیت زمینه فلزی چیست؟
در فرآیند ساخت کامپوزیتهای زمینه فلزی (Metal Matrix Composite) یا به اختصار MMC، از یک قطعه فلزی مثل آلومینیوم به عنوان زمینه خود استفاده میکنند و الیافهای مختلفی مثل سیلیکون، به عنوان تقویتکننده با آن ترکیب میشوند. کامپوزیتهای زمینه فلزی با اینکه مدت کوتاهی است که وارد بازار شدند و نسبت به رقبای خود سابقه کمتری دارند، اما موفق شدند جایگاه خود را در بازار پیدا کنند.
دلیل کاربرد فراوان کامپوزیت پایه فلزی، علاوه بر خواص آن، هزینه کمتری است که نسبت به سایر کامپوزیتها دارد. این روزها قیمت انواع ورق با نوسانات زیادی مواجه است و همین امر روی قیمت سایر مواد هم تاثیر میگذارد. اما با وجود این نوسانات هم قیمت کامپوزیت پایه فلزی نسبتا معقول است.
انواع کامپوزیت زمینه فلزی
فلزهای گوناگونی به عنوان زمینه در این کامپوزیت به کار گرفته میشوند و همین امر موجب گستردگی کاربردها و ویژگیهای آن شده است. انواع پایههای فلزی مورد استفاده در این کامپوزیتها به شرح زیر است:
- پایه مس
- پایه تیتانیوم
- پایه منیزیم
- پایه آهن
- پایه آلومینیوم
- پایه نیکل
هر کدام از این پایهها هم خصوصیت خاصی را به کامپوزیت اضافه میکنند تا بتوان در صنایع مختلف از آن بهرهمند شد. فرآیند تولید هرکدام از این کامپوزیتها هم تقریبا متفاوت است. کامپوزیتهای پایه فلزی در انواع خود، مراحل دقیقی را برای تولید طی میکنند، چرا که در صنایع حساسی مثل هوافضا استفاده میشوند و کوچکترین خطا در این صنایع میتواند خسارات جبرانناپذیری را به همراه داشته باشد.
خواص و تفاوت کامپوزیتهای پایه فلزی نسبت به سایر مواد مرکب
کامپوزیتهای فلزی نسبت به سایر انواع کامپوزیت فرآیند متفاوتی را طی میکنند. پایهی آلومینیوم و منیزیم به نسبت دیگر فلزات مورد استفاده به عنوان زمینه خواص بیشتری دارند. چگالی بسیار پایین، استحکام زیاد، قابلیت ریختهگری، قابلیت ماشینکاری و دسترسی فراوان از دلایلی است که این دو فلز به همراه آلیاژهایشان را به پر کاربردترین فلزات کامپوزیتهای پایه فلزی تبدیل کرده است. البته معایبی را نیز به همراه خود دارند که از جمله آنها به مقاومت سایشی کم میتوان اشاره کرد.
اگر بخواهیم کامپوزیتهای زمینه فلزی را به صورت کلی با دیگر انواع مقایسه کنیم، باید بگوییم که هر کدام از کامپوزیتها ویژگی دارند که با توجه به شرایط و نحوه استفاده شما میتوانند مفید واقع شوند. پس بهتر است نام این مقایسه را بیان تفاوتها بگذاریم. بدین صورت با فهمیدن این اختلافات میتوانید برای خود تصمیم بگیرید که کدام برای شما مناسبتر است.
- کامپوزیتهای پایه فلزی نسبت به کامپوزیتهای زمینه پلیمری از ظرفیت گرمایی بالاتر و نسبت به کامپوزیتهای زمینه سرامیکی از ظرفیت گرمایی پایینتری برخوردارند.
- تقویتکنندهها مورد دیگری است که انواع کامپوزیتها در آن با یکدیگر اختلاف دارند. به عنوان مثال تقویتکننده مورد استفاده در ترکیب کامپوزیت زمینه سرامیکی باعث کاهش احتمال تاب برداشتن میشود، در حالی که تقویتکنندههای زمینه فلزی باعث افزایش استحکام و مقاومت پایه میشوند.
- در کامپوزیتهای فلزی، جنس زمینه یک فلز آلیاژی یا خالص است، برعکس دو نوع دیگر که پلیمر یا سرامیک جنس زمینه را تشکیل میدهند.
روشهای ساخت کامپوزیتهای زمینه فلزی
کامپوزیت زمینه فلزی در سه روش تولید و ساخته میشود:
- روش مایع یا ریختهگری
- روش متالوژی پودر
- روش آلیاژسازی مکانیکی
هر کدام از این روشها، در چند مرحله ابتدایی که برای تولید باید انجام شود، عملکرد تقریبا یکسانی دارند و مراحل مشابهی را طی میکنند. در مراحل پیش فرآیند، فرآیند اولیه و ثانویه تقریبا تمامی روشهای تولید کامپوزیت زمینه فلزی، هممسیر هستند و بعد از آن است که نحوه ایجاد هرکدام فرق میکند. در ادامه هر کدام را به صورت جداگانه بررسی خواهیم کرد:
تولید کامپوزیت زمینه فلزی: روش مایع یا ریختهگری
در روش ریختهگری، ذرات تقویتکننده به فلز مذاب اضافه شده و به صورت مکانیکی در داخل فلز توزیع میشوند. اغلب کامپوزیتهای پایه فلزی با این روش تولید میشوند. کامپوزیت مایع حالت آبکی دارد و در قالبهای گوناگون ریخته میشود تا برای انجام مراحل نهایی آماده شود. بزرگترین و مهمترین مزیت این روش، تولید کامپوزیت با هزینه پایین است. اما معایبی را هم مثل عدم مرطوب کردن ذرات تقویتکننده توسط آلومینیوم مایع است که باعث میشود تا ذرات به صورت غیریکنواخت توزیع شوند یا ذرات از فلز مذاب جدا شوند.
برای حل این مشکل فلز مذاب را درون تراوری میکنند و با مخلوط کردن دسته الیافها با فلز مذاب، ذرات را درون آن جای میدهند. این فرآیند به صورتهای مختلفی میتواند انجام شود. ریختهگری هم انواع مختلفی دارد که با استفاده از آن مدلهای گوناگونی از کامپوزیت پایه فلزی را تهیه میکنند.
- ریختهگری فشاری Squeeze casting
ریختهگری فشاری یا کوبشی، جز مراحل اولیه فرآیند شکلدهی فلز است. در طول انجام این فرآیند، مقدار مشخصی از فلز مذاب داخل قالبها ریخته میشود و تحت فشار زیاد، در معرض انجماد قرار میگیرد تا محصولی با دقت بسیار بالا تولید شود.
فرآیند ریختهگری فشاری نیازمند کنترل دقیق متغیرهای فرآیند است تا از بروز اشکالات مختلف مثل تغییر شکل ساختار اولیه جلوگیری کند. به همین خاطر ریختهگری فشاری روش بسیار مناسبی برای تولید قطعات ماشین یا هر قطعهای که شکل پیچیدهای دارد و باید سریع تولید شود، است.
- روش همنشت پاششی Spray co-deposition method
همنشت پاششی یکی از روشهای اقتصادی تولید کامپوزیت زمینه فلزی است. با این روش، محصول به دست آمده کامپوزیت ذرهای خواهد بود. این روش را کمتر استفاده میکنند و جز روشهایی است که محبوبیت زیادی ندارد.
- ریختهگری تلاطمی Stir casting
ریختهگری تلاطمی، مقرونبهصرفهترین و سادهترین روش برای تولید کامپوزیتهای زمینه فلزی است. این روش، مخلوطی از ذرات تقویتکننده داخل فلز مذاب ایجاد میشود. سپس این مخلوط توسط همزن، یکنواخت میشود تا بتواند به صورت مستقیم به قالب خود انتقال یابد. در این روش هم یکی از معضلاتی که وجود دارد، ایجاد رطوبت بین ذرات تقویتکننده و فلز مذاب است
- ریختهگری ترکیبی Compo casting
ریختهگری ترکیبی روش اصلاح شده ریختهگری تلاطمی بوده و برای ساخت کامپوزیت با الیاف ناپوسته کاملا مناسب و مقرونبهصرفه است.
تولید کامپوزیت زمینه فلزی: روش متالوژی پودر
روش متالوژی پودر، روش دیگری است که برای تولید کامپوزیت زمینه فلزی استفاده میشود. این روش معمولا برای ساخت کامپوزیت با الیاف ناپوسته به کار میرود. ابتدا پودرهایی از مواد زمینه و تقویتکننده را با یکدیگر مخلوط میشوند، سپس داخل قالبی ریخته میشوند. پس از این مرحله، برای اتصال بهتر پرسکاری سرد صورت میگیرد. بعد ذرات به هم پیوسته تا درجه حرارتی که زیر نقطه ذوب آنها باشد، گرما میبینند. در نهایت طی فرآیند کوتاهی کامپوزیت ایجاد میشود.
این روش نسبت به سایر روشها مطمئنتر است و به همین علت، طرفداران زیادتری هم دارد و بیشتر مورد استفاده قرار میگیرد. متالوژی پودر به مراتب گرانتر هم هست و علاوه بر آن توزیع درست ذرات هم کار دشواری است و باید دقت زیادی در تولید آن شود؛ وگرنه ممکن است چقرمگی، شکست و دیگر عوامل زیانآور زودتر از آنچه فکر میکنید، پیدا شوند.
تولید کامپوزیت زمینه فلزی: روش آلیاژسازی مکانیکی
آلیاژسازی مکانیکی را شاید بتوان مهمترین روش تولید نانوکامپوزیتهای زمینه فلزی دانست. در این روش، ذرات نانوپودری دو فاز با یکدیگر آسیاب میشوند و با تغییر شکل، جوش خوردن و شکست ذرات به صورت مکرر انتقال مواد صورت میپذیرد.
اگر ذرات نانوپودر ترکیب شیمیایی یکسانی داشته باشند و با انجام عملیات فقط اندازه ذرات کاهش یابد، فرایند آسیای مکانیکی اتفاق میافتد. اما چنانچه آسیای مکانیکی با انجام واکنش شیمیایی در حالت جامد_جامد و یا جامد_گاز همراه باشد، فرآیند آسیای واکنشی نامیده میشود. در ادامه بیشتر درباره نانوکامپوزیتها و البته نانوکامپوزیت زمینه فلزی صحبت خواهیم کرد.
برای ساخت پودرهای کامپوزیتی با افزودن مستقیم ذرات فاز تقویتکننده میتوان به ذرات زمینه و آسیای این ذرات، نانوپودرهای کامپوزیتی تهیه کرد. با افزایش زمان آسیاب کردن تحت انرژی زیاد، میتوان ابعاد فاز تقویتکننده و حتی اندازه دانههای زمینه را تا حد نانومتر کاهش داد. قابل ذکر است که آسیای مکانیکی همزمان، توزیع یکنواختی از ذرات نانومتری تقویتکننده در فاز زمینه را ایجاد میکند.
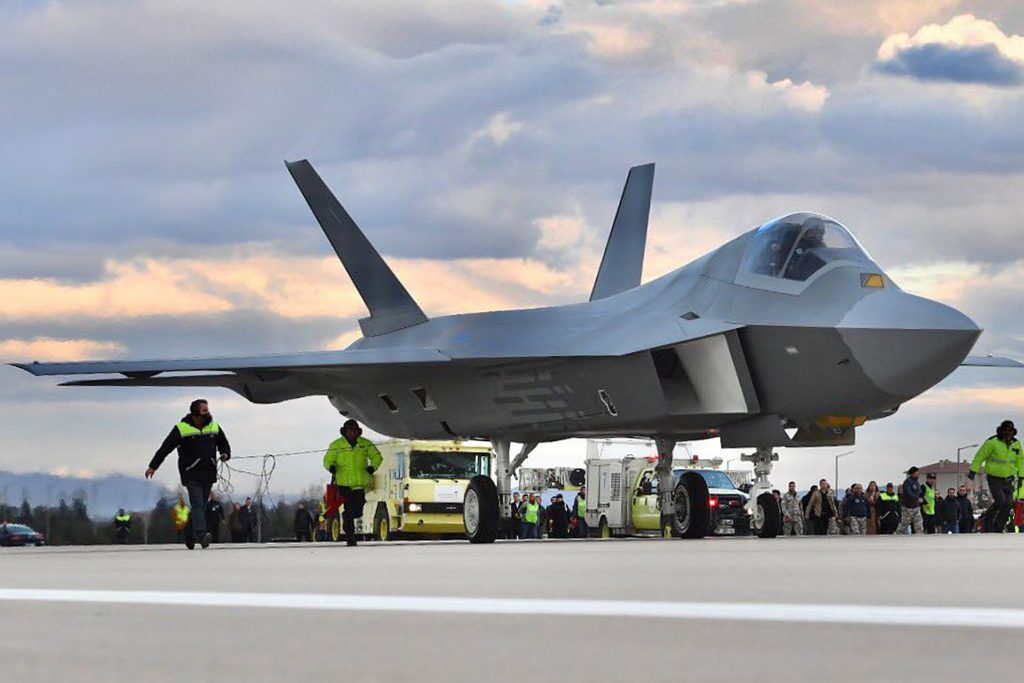
کاربردهای Metal Matrix Composite
کامپوزیتهای زمینه فلزی همانطور که گفته شد، از پرکاربردترین کامپوزیتهایی هستند که در صنایع مختلف مورد استفاده قرار میگیرند. بیشترین استفاده آنها در صنعت هوافضا و صنعت خودروسازی است. در سالیان گذشته و با ورود و گسترش قطعات نانوکامپوزیت که زمینه فلزی دارند، این مواد بیش از پیش مورد استقبال صنعتگران مخصوصا در حوزه خودرو قرار گرفته است.
در ایران به دلیل هزینههای بالایی که برای خودروسازان به همراه دارد، از کامپوزیتهای پلیمری استفاده میکنند که به مراتب کیفیت کمتری را ارائه میدهند. اما در کشورهای پیشرفته و پیشرو در صنعت خودرو و خودروسازی مثل آلمان و آمریکا، از کامپوزیت و نانوکامپوزیتهای فلزی استفاده میکنند تا در برابر ضربه، و انواع تخریبهای شیمیایی از خود مقاومت نشان دهد. در اصل یک نوع لایه محافظ برای ماشین است که علاوه بر استحکام فوقالعادهای که دارد، وزن بسیار سبکی هم دارد.
به عنوان مثال، تصور کنید که دو ماشین با یکدیگر برخورد کردند، ماشینی که از کامپوزیت پلیمری استفاده کرده باشد، بدنهاش فرو میرود و به اصطلاح قر میشود. اما در ماشینی که از کامپوزیت و نانوکامپوزیتهای فلزی استفاده شده باشد، آسیب به مراتب کمتری مشاهده خواهد شد.
کاربرد دیگری که کامپوزیتهای پایه فلزی دارند، در صنعت هوافضا است. جایی که برای ساخت تلسکوپهای فضایی و انواع هواپیماها مثل تکسرنشین، مسافری، جنگنده و… استفاده میشود. در هواپیماها برای افرایش استحکام و در عین حال داشتن وزن مناسب برای پرواز استفاده میشود.
پیدایش نانوکامپوزیت زمینه فلزی
در زمان قدیم، برای تقویت استحکام و افزایش مقاومت در فلزات و آلیاژها اجزای غیرفلزی مثل سرامیک استفاده میکردند تا بتوانند در برابر عوامل تخریب و کاهش خواص مکانیکی اثرگذار باشند. اما در چند دهه گذشته، پودر گرافیت با پوشش نیکل را بهوسیله جریان گاز آرگون، در مذاب آلیاژ آلومینیوم وارد کردند. این فرآیند در واقع شروع تولید کامپوزیتهایی با زمینهی فلزی بود که در آن زمان به MMPC مشهور شدند.
بعد از گذشت چندین سال، دانشمندان و محققان موفق شدند که کامپوزیتها را با تکنولوژی نانو ترکیب کنند تا موادی که به دست میآیند، کارایی بیشتری داشته باشند.
نانوکامپوزیت یعنی کامپوزیتی که حداقل یکی از اجزای تشکیلدهنده آن ابعادی بین ۱ تا ۱۰۰ نانومتر داشته باشد. فاز اول یک ساختار بلوری شکل است که در اصل پایه یا زمینه نانوکامپوزیت محسوب میشود که همانطور که میدانید علاوه بر فلز، میتواند پلیمر یا سرامیک هم باشد. فاز دوم هم شامل ذراتی در مقیاس نانومتر است که به عنوان تقویتکننده درون فاز اول که زمینه باشد، توزیع میشوند. ذرات تقویتکننده در اینجا نقش پرکننده دارند و برای افزایش استحکام، مقاومت، خواص مغناطیسی و… این کار انجام میدهند.
نانوکامپوزیتها کاربردهای فراوانی را به صنایع مختلف اضافه کردند. برای مثال در صنعت خودرو باعث ۲۰ درصد کاهش وزن ماشینها شدند. در صنعت بستهبندی در نایلونها باعث دوام بیشتر مواد داخل نایلون شدند، به دلیل اینکه از خروج کربن دیاکسید جلوگیری میکند. همچنین در موارد دیگری همچون توپ تنیس، پوششهای کابل، لاستیک، سیمهای عایق، حسگرهای محیطی و… مورد استفاده قرار میگیرند.
جمعبندی
کامپوزیتها در انواع مختلفی وجود دارند و باعث ایجاد مزایای فراوانی در زندگی انسانها شدند. در این مقاله به معرفی بیشتر یکی از انواع کامپوزیتها یعنی کامپوزیت زمینه فلزی پرداختیم و آن را از جنبهها و جهات مختلف مورد بررسی قرار دادیم. امیدواریم که این مقاله موجب آشنایی بیشتر شما با این موضوع شده باشد و حتما در بخش نظرات برای ما از تجربیات استفاده از کامپوزیتهای پایه فلزی و کاربردهای دیگری که از آن سراغ دارید، بنویسید.