همانطور که میدانید فلز مس از انعطافپذیری بالایی برخوردار بوده و همچنین رسانایی گرمایی و الکتریکی زیادی دارد. ویژگیهای منحصر به فرد این فلز سبب کاربردهای متنوع و به شکلهای مختلف در صنعت شده است. یکی از پرکاربردترین فرمهای تولید فلز مس، به صورت لوله و اتصالات است. لوله مسی استوانهای توخالی است که از نظر جنس، کاربرد و سایز به انواع مختلفی تقسیم میشود. این محصول به لحاظ کاربرد به دو دسته تفکیک میشود؛ لولههای مورد استفاده در انواع لولهکشی مانند لولهکشی آب و گاز، لولههای مسی که در دستگاههای تهویه مطبوع مورد استفاده قرار میگیرند. مانند لولههای مورد استفاده در کولرهای گازی. لوله و اتصالات مسی به شکل زانو، تبدیل، بوش، سه راهی و… تولید میشود.
مزیتهای لوله مسی از جمله توزیع دمای یکنواخت در بدنه، قابلیت شکلپذیری بالا، قابلیت بازیافت، سازگاری با محیط زیست، هزینه پایین تولید و مقاومت در برابر فشار و تنش فیزیکی است که سبب استفاده هر چه بیشتر آن در صنایع مختلف شده. دوام و طول عمر بالای لوله و اتصالات مسی سبب صرفهجویی در هزینه در درازمدت خواهد شد. امروزه مصرف لوله مسی در سراسر جهان رو به افزایش است. برای انتخاب لوله مسی ابتدا لازم است با برندهای مختلف و چند کارخانه لوله مسی در کشور آشنا شده و سپس با مقایسه خصوصیات و مزیتهای هر کدام و همچنین کاربرد مورد نظر، اقدام به انتخاب بهترین لوله مسی کنیم. اگر هنگام انتخاب لوله مسی تردید داشته و یا دچار اشتباه میشوید، با این مقاله از آهن الات نوین ارکا همراه شوید.
برای انتخاب لوله مسی ابتدا لازم است با برندهای مختلف و کارخانههای تولیدکننده لوله مسی در کشور آشنا شده و سپس با مقایسه خصوصیات و مزیتهای هر کدام و همچنین کاربرد مورد نظر، اقدام به انتخاب بهترین لوله مسی کنیم.
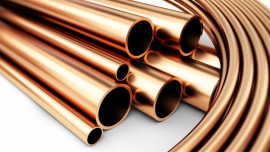
کارخانههای تولیدکننده لوله مسی
کشور ایران دارای منابع بسیار غنی از مس است. عمده معادن این فلز در سرچشمه کرمان قرار دارد و در زمره بهترین معادن مس جهان طبقهبندی میشود. شرکت ملی مس ایران با ظرفیت تولید ۴۰۰ هزار تن کاتد مسی در سال به عنوان متولی فروش مس خام به صنایع پایین دستی مشغول فعالیت است و این مقدار مس خام به معنای تامین مواد اولیه لازم برای تمام صنایع پایین دستی مس در کشور است. به همین جهت مراکز متعدد تولید لوله مسی در کشور مشغول به فعالیت هستند که انواع مختلفی از این محصول را تولید و عرضه میکنند. قیمت لوله مسی از برند و کارخانه تولیدکننده آن و استانداردهای رعایت شده هنگام تولید محصول نیز متاثر میشود. در ساخت لولههای مسی استانداردهای بینالمللی مانند ASTM و مورد استفاده قرار میگیرد. در این استانداردها خواص فیزیکی و شیمیایی لوله مانند اندازه دانه، ازدیاد طول نسبی، سختی و میزان کشش لوله، چگالی، میزان هدایت الکتریکی و حرارتی، مقاومت الکتریکی، حالت سختی و آلیاژ مشخص شده است. در ادامه به معرفی کارخانههای تولیدکننده لوله مسی و مشخصات هر کدام از آنها خواهیم پرداخت.
کارخانه لوله مسی مهر اصل
این کارخانه در سال 1369 در شهرک صنعتی سلیمی آذربایجان شرقی تاسیس شد. واحد تولیدی مهر اصل با سالنهای تولید عملیاتی بیش از ۴۰ هزار متر مربع به عنوان بزرگترین تولیدکننده کویل در ایران مشغول به فعالیت است. این کارخانه تولیدکننده دستگاهها، قطعات و تجهیزات صنعتی حرارتی، برودتی و تهویه مطبوع بوده و دارای هفت خط کامل اتوماتیک تولید کویل بوده و تغذیهکننده اکثر کویلهای کارخانجات تهویه مطبوع بوده و همچنین بزرگترین تولیدکننده داخلی کولرهای گازی صنعتی و خانگی است. مجموعه تولیدی مهر اصل به عنوان مجهزترین تولیدکننده لوله مسی مورد نیاز صنعت تهویه مطبوع کشور شناخته شده است. چیلرهای جذبی دو اثر تحت لیسانس و با نشان Kawasaki ژاپن، از دیگر تولیدات این کارخانه است. تولیدات این مجموعه صنعتی به همراه تعداد تقریبی آنها در سال شامل موارد زیر است:
- چیلر (۸۰۰ دستگاه)
- چیلر جذبی (۲۰۰ دستگاه)
- انواع برجهای خنککننده (۱۵۰۰ دستگاه)
- پکیج یونیت حساس (۱۰۰۰ دستگاه)
- هواساز (۱۰۰۰ دستگاه)
- پکیج یونیتهای هوایی (۲۰۰ دستگاه)
- فن کویل (۱۰۰ هزار دستگاه)
- کولرهای گازی صنعتی و خانگی (۲۱۰ هزار دستگاه)
- یونیت هیتر (۴۰۰۰ دستگاه)
- مبدل حرارتی (۸۲۵ دستگاه)
- انواع کندانسور و مبدل حرارتی (۲۰ هزار دستگاه)
- انواع اواپراتور و مبدل حرارتی (۲۰ هزار دستگاه)
- دستگاه تهویه مطبوع هواپیما (۶۰ دستگاه
- عایق حرارتی (۴۵۰ هزار دستگاه)
کارخانه مهر اصل تولید کننده انواع لوله مسی (۱۰ هزار تن در سال) و انواع اتصالات لوله مسی (۲۰۰ تن در سال) است. این کارخانه جز مجهزترین و مدرنترین کارخانههای تولید لوله مسی در منطقه خاورمیانه است و محصولات خود را در انواع کویل، شاخهای، کلاف و شیاردار داخلی، فیندار بیرونی در اندازههای مختلف و بر طبق استانداردهای بینالمللی به خصوص استاندارد ASTM B280 به بازار ارائه میکند. لولههای فیندار درونی برای دستگاههای خنکشونده تزریق مستقیم و سیالات توسط شرکت مهراصل طراحی و ساخته شده است. این محصول در قسمتهایی که سیال در بیرون لولهها سرد میشود و یا در مواردی که سیال یا مبرد عامل در داخل لوله، تبخیر یا تقطیر میشود، مورد استفاده قرار میگیرد. ضریب تبادل حرارتی متوسط داخلی این نوع لوله نسبت به لولههای ساده ۱/۵ تا ۲/۵ برابر بیشتر است. به این ترتیب لوله کمتری جهت تامین انتقال حرارت داخل لوله مصرف میشود. این محصول در انواع مختلف کویل، کلاف، شاخه و به صورت سخت و نرم قابل ارائه است.
تولید لوله مسی در این کارخانه با ذوب کاتد مسی در کوره القایی آغاز میشود. پس از ریختهگری مداوم پوسته مادر، وارد مرحله نورد برای اصلاح ساختار کریستالی و پس از آن، لوله مادر وارد خطوط کشش سه مرحلهای میشود. مرحله آخر، کشش در ماشین دورانی است. در این مرحله لوله به یکی از اشکال کلاف، شاخه و یا کویل درمیآید. آنیل کردن روی تمام محصولات برای حذف تنشهای آن انجام میشود و سپس نوبت به بستهبندی و حمل محصولات میرسد. کنترل کیفیت لولههای مسی در این کارخانه شامل تجزیه ترکیبات مذاب و شناسایی مواد تشکیلدهنده آن، تشخیص سطوح معیوب لوله حین تولید و جداسازی آنها از تولیدات قابل تحویل، اندازهگیری ارتفاع فینها و دندانه لوله به طور دقیق، آزمایش کشش لوله جهت تعیین وضعیت مکانیکی، اندازهگیری مقدار روغن و کربن و تشخیص مطابقت آنها با استانداردها و اندازهگیری دانهبندی و سایز کریستالها میشود.
شرکت صنایع مس قائم
این شرکت در سال ۱۳۸۳ در شهرک صنعتی مورچه خورت اصفهان تاسیس شد. سالن تولید این کارخانه دارای تجهیزات مدرن تولید لوله مسی و تامین سالانه 24 هزار تن محصول لوله مسی به شکلهای کویل، کلاف، شاخه و شیاردار است. تمام محصولات این شرکت از آلیاژهای مسی DHP و ETP که از بهترین رده کاتد مس با خلوص ۹۹/۹ درصد به دست میآیند، تامین میشود. این شرکت در تولید لوله مسی بدون درز از تکنولوژی C&R که ابداعی شرکت اتوکومپوی فنلاند در دهه ۹۰ میلادی است، بهره میبرد. این روش از مرحلههای اساسی ذوب، ریختهگری و نورد تشکیل میشود. سطوح خارجی پوستههای به دست آمده از فرآیند ریختهگری، جهت جدا کردن لایه اکسید سطحی، پوستهبرداری میشوند. در حین فرآیند نورد از هیچگونه روغن و روانکاری استفاده نمیشود. به همین جهت و همچنین به دلیل استفاده از گاز خنثی، سطوح داخلی و خارجی کاملا شفافی حاصل میشود که منجر به خواص مکانیکی بهتر محصول نهایی میشود.
محصولات این شرکت در سایزها و به شکلها و بستهبندیهای مختلفی قابل عرضه هستند. از آن جایی که تمیز بودن سطح داخلی لولهها در عملکرد دستگاههای مصرفکننده تاثیرگذار است، به داخل آنها گاز خنثی تزریق کرده و هر دو سمت آن بسته میشود. در مراحل کنترل کیفیت محصول خروجی این کارخانه، تستهای جریان گردابی که غیریکنواختی در سطوح داخلی و خارجی لوله را آشکار میکند، تست کوانتومتر جهت تعیین عناصر موجود در نمونه، تست کشش جهت بررسی خواص مکانیکی و بررسی توسط میکروسکوپ نوری برای اندازهگیری هر دو پارامتر اندازه دانه و مشخصات ابعادی لولههای داخل شیاردار، انجام میشود.
شرکت صنایع مس باهنر
کارخانه صنایع مس با هنر در دوازده کیلومتری شهر کرمان قرار گرفته است. این شرکت که در نیمه دوم سال ۱۳۷۰ تاسیس شد، بزرگترین مجتمع صنعتی ارتباطدهنده معادن مس و روی کشور، با صنایع تولیدی به شمار میرود و شامل پنج کارخانه ذوب و ریختهگری، نورد، اکستروژن و کشش، سکهزنی و لوله مسی است. کارخانه لوله مسی این مجموعه در سال ۱۳۸۶ با هدف تولید سالانه ۱۵ هزار تن لوله مسی، شروع به فعالیت کرد. این مجموعه گستردهترین محصولات مسی و آلیاژهای آن را به صورت ورق (کویل، تسمه و فویل)، لوله (شاخه، کویل، پن کیک) و مقاطع (سه گوش، چهارگوش، شش گوش و میلگرد توپر و توخالی) تولید میکند.
لوله مسی صنایع مس باهنر بنا به نیاز بازار در سه گروه DLPT، TPC ، DHP تولید میشود. لوله مسی TPC به دلیل دارا بودن هدایت الکتریکی بسیار بالا، مصرف الکتریکی داشته و در تولید انواع کابل از این نوع لوله مسی استفاده میشود. دو نوع دیگر لوله تولید این مجموعه علاوه بر هدایت الکتریکی بالا، قابلیت جوشکاری مناسبی داشته و از این رو در تولید مبدلهای حرارتی کاربرد دارد. این کارخانه در تولید لولههای مسی از تکنولوژی cast&roll بهره میبرد که از بروزترین روشهای تولید لوله مسی است. همه تجهیزات این کارخانه از گروه شرکتهای آلمانی SMS-MEER خریداری شده است. این مجموعه شامل بخشهای ذوب و ریختهگری، پوستهبرداری (به هدف تولید محصول براق و عاری از اکسید)، نورد به وسیله دستگاه سیارهای، کشش به وسیله ماشینهای کشش، شیارزنی برای افزایش ضریب انتقال حرارت، ترازپیچ و بررسی لوله به وسیله دستگاه تست غیرمخرب ادی-کارنت و آنیل به هدف ایجاد خواص مکانیکی و متالورژی مطلوب در محصول است.
شرکت بابک مس ایرانیان
این شرکت در سال ۱۳۹۰ پروژه احداث خط تولید لوله مسی به روش Cast Draw را آغاز کرد. این روش از جمله جدیدترین و پیشرفتهترین روشهای تولید لوله مسی در جهان است که با تغییرات تکنولوژی ایجاد شده، فرآیند تولید لوله را کوتاه کرده و در نتیجه قیمت تمام شده محصول را کاهش داده است. تکنولوژی ریختهگری این کارخانه جز پیشرفتهترین تکنولوژیهای روز دنیا است که از شرکت UP Cast فنلاند خریداری شده است. همچنین تجهیزات کشش لوله آن از ASMA اتریش خریداری شده است. لوله مسی تولیدی این کارخانه با بهترین کیفیت و مطابق استانداردهای روز دنیا از جمله ASTM B280 است که میتواند نیاز کامل صنایع داخلی و خاورمیانه را تامین کند. انواع لوله مسی بابک مس ایرانیان قطری در بازه تا ۶ تا ۲۷ میلیمتر داراست.
در فرآیند تولید این محصولات ابتدا ریختهگری انجام میشود و پس از آلیاژسازی مناسب، مذاب به کوره القایی نگهدارنده منتقل میشود و سپس به روش ریختهگری سربالا، لولههای مادر با ابعاد مخصوص مستقیما ریختهگری شده و به سبدهای مخصوص منتقل میشوند. قطر و ضخامت لولههای مادر توسط دستگاه کشش کاهش مییابد. مرحله آنیل میانی برای آزادسازی تنشهای لوله انجام میشود. جهت سایزکردن نهایی، لولههای کشیده شده در مرحله قبل، به دستگاه کشش ثانویه اسپینر بلاک منتقل میشوند. سپس لولههایی که باید به بازار عرضه شوند به ماشین ترازپیچ منتقل میشوند تا لوله از دستگاه ادی کارنت عبور کرده و نقاط معیوب آن مشخص شود. سپس لوله به صورت کویلهای ۱۰۰ تا ۱۵۰ کیلوگرمی پیچیده میشود.
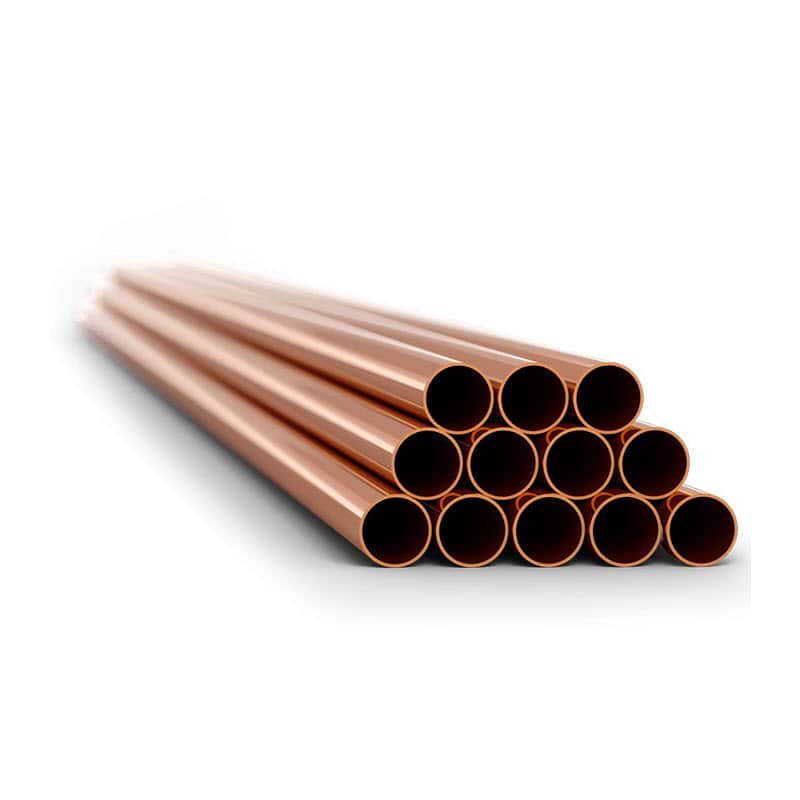
جمعبندی
با توجه به مطالب عنوان شده با برندهای مختلف تولیدکننده لوله مسی آشنا شدیم. شناخت برند، استانداردهای رعایت شده در ساخت، نوع لوله مسی و روش ساخت آن میتواند کمک کند تا انتخاب صحیحی مطابق با کاربرد مورد نظر داشته باشیم. شما نیز اگر در استفاده از انواع برندهای لوله مسی تجربهای دارید، در قسمت کامنت با ما به اشتراک بگذارید.